Future Production Technologies
Welcome to the Future Production Technologies page. Here, we will highlight new approaches for coating and drying in battery production, with a focus on improving energy efficiency and reducing costs. In the future, we’ll be assessing different future production technologies.
Technologies under assessment:
- Mixing:
- Continuous mixing (extrusion)
- High-speed tumbler mixing
- Dry Coating:
- Electrostatic spraying
- Brush application
- Electrostatic fluidized bed deposition
- Extrusion-based coating
- Free-standing electrode fabrication
- Direct calendaring
- Laser Drying:
- VCSEL (Vertical-Cavity Surface-Emitting Laser)
- Diode laser drying
- NIR-Drying (Near-Infrared Drying)
- Pre-lithiation
- Roll-to-Roll Vacuum Drying
- Multilayer Coating
- Rotative High-Speed Single Sheet Stacking
- Mini Environments
More technology assessments coming soon…
We will be adding future production technologies to our website in the future, so stay tuned for upcoming updates.
Dry Coating
Impact on Processstep
Cost
X%
Sustainability
X %
Quality
X %
Output
X %
Workforce
X %
Others
X %
TRL: 4
Impact on Production
Coating & Drying
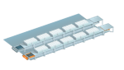
Suitable Formats
Prismatic
Cylindrical
Pouch
Description
In order to make the electrode production process more effective, an attempt is made to work without or with only a small amount of solvent. There are different types of processing (extrusion, direct calendering process, powder application and single layer application). Dry coating has advantages in terms of energy consumption. No or only a reduced amount of toxic solvents is used and the plant’s environmental footprint is much smaller. Dry coating still faces challenges because of the impact on up-stream and downstream processes, the adhesion of active material to the current collector foil, and binder processing.
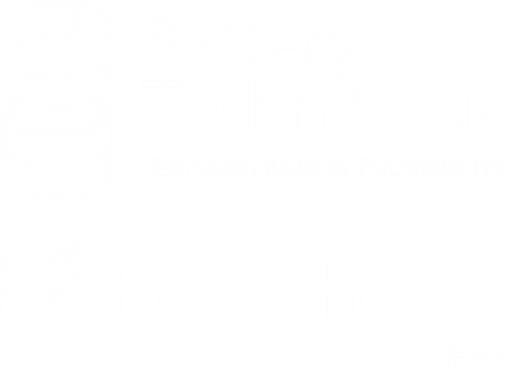
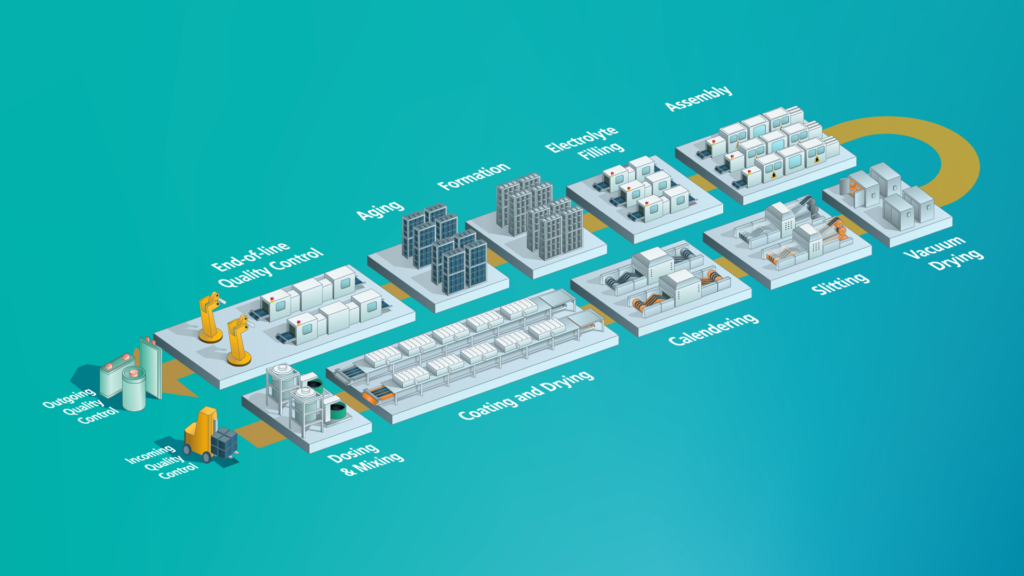