More heatmaps
coming soon...
... including heatmap of workforce and heatmap of machine output
Battery Cell Production Layout
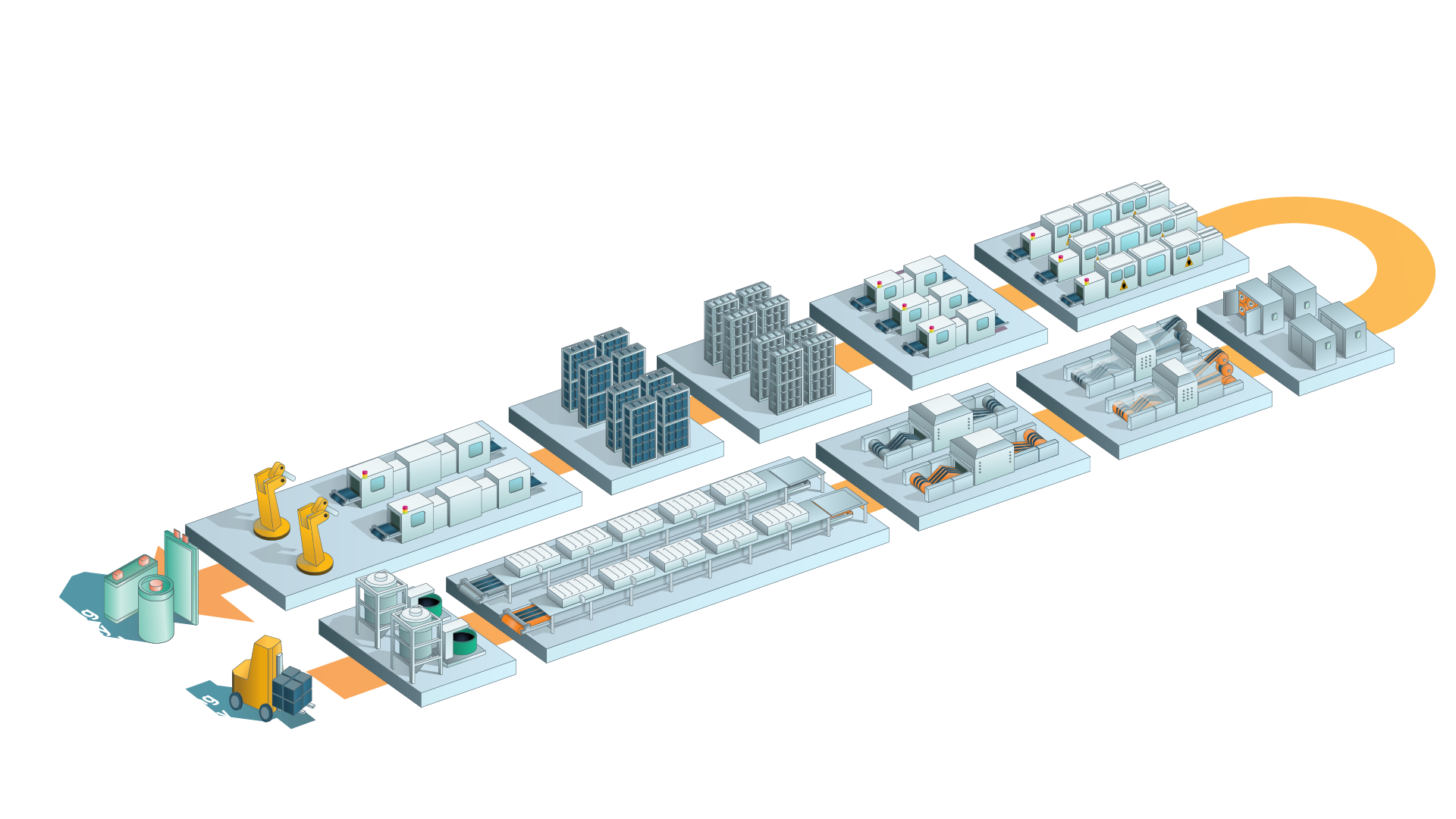
Lithium-ion-batteries are one of the most widely used energy storage technologies today, ranging from smartphones and laptops to electric vehicles and grid-scale energy storage systems. The production of lithium-ion-batteries involves several steps, including the manufacture of electrodes, the assembly of cells and the integration of cells into battery packs. The manufacturing process begins with the preparation of electrode materials, usually using a combination of powders, binders, and solvents. The materials are mixed together and coated onto thin metal foils, which are then dried and rolled into electrode sheets. The electrode sheets are then cut to size and assembled into a cell with the other components (separator, electrolyte,…). Once the cells are assembled, they are tested to ensure that they meet certain performance criteria, such as capacity, energy density, and cycle life.
Heatmap of Cost (CapEx)
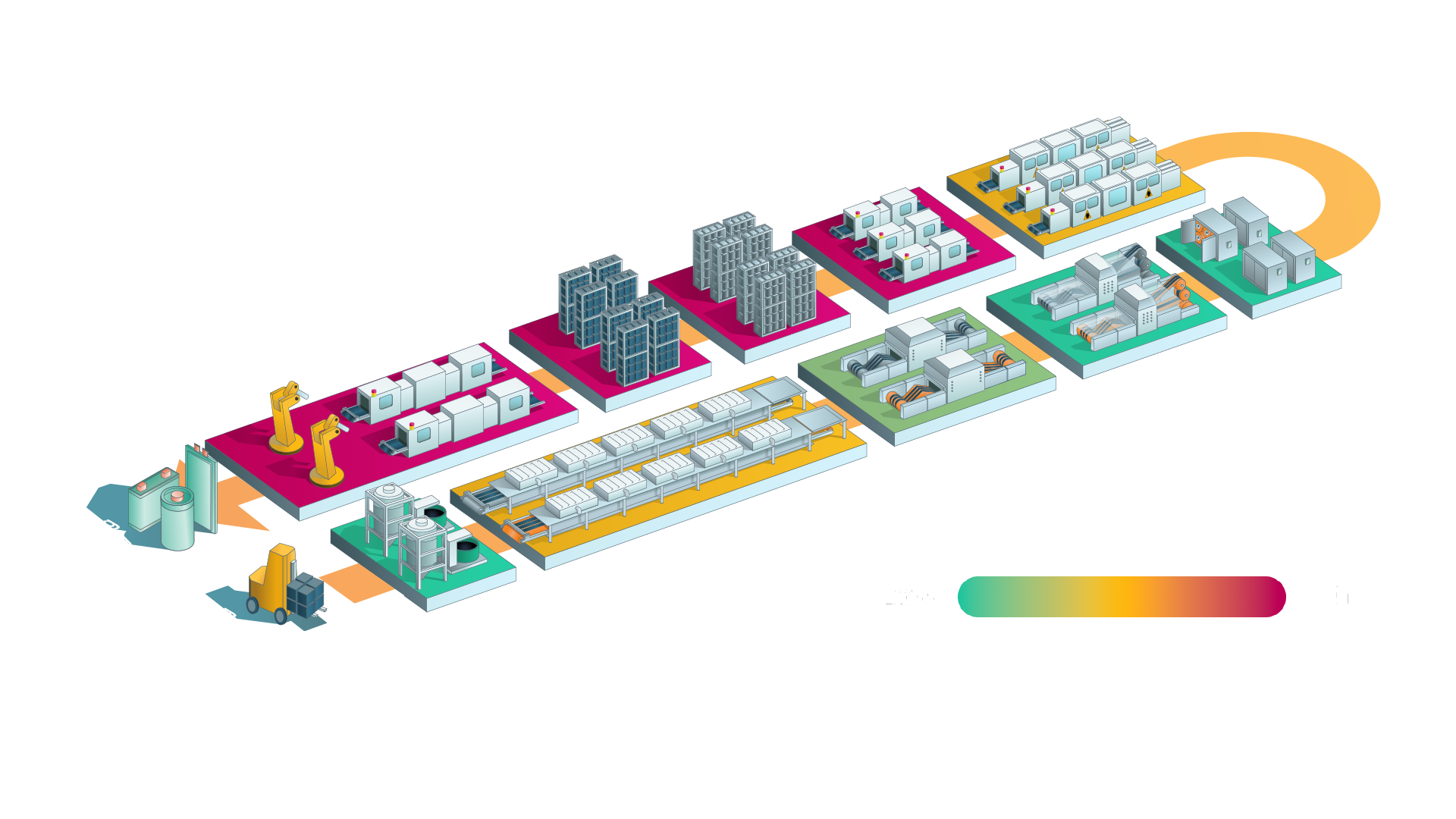
Many different electronic devices, such as electronic storage systems, mobile technology or electric vehicles are linked to the production of battery cells. In this context, reducing costs in battery cell production plays an important role in order to remain competitive. The following aspects are the main cost drivers in battery cell production:
- raw materials (e.g. lithium, cobalt, nickel)
- production method (e.g. automation, innovative technologies)
- energy consumption, labor costs and quality assurance
Overall, the costs of battery cell production are caught between technological progress, economic efficiency, and environmental responsibility.
The investment cost for the production equipment ranges from €22 million to €100 million per GWh of battery cell production capacity per year.
CapEx costs in electrolyte filling, formation, aging, and end-of-line quality control production steps of battery cells are significant, encompassing specialized equipment, automation systems, and quality assurance technologies essential for ensuring high performance and reliability.
Heatmap of Energy Consumption
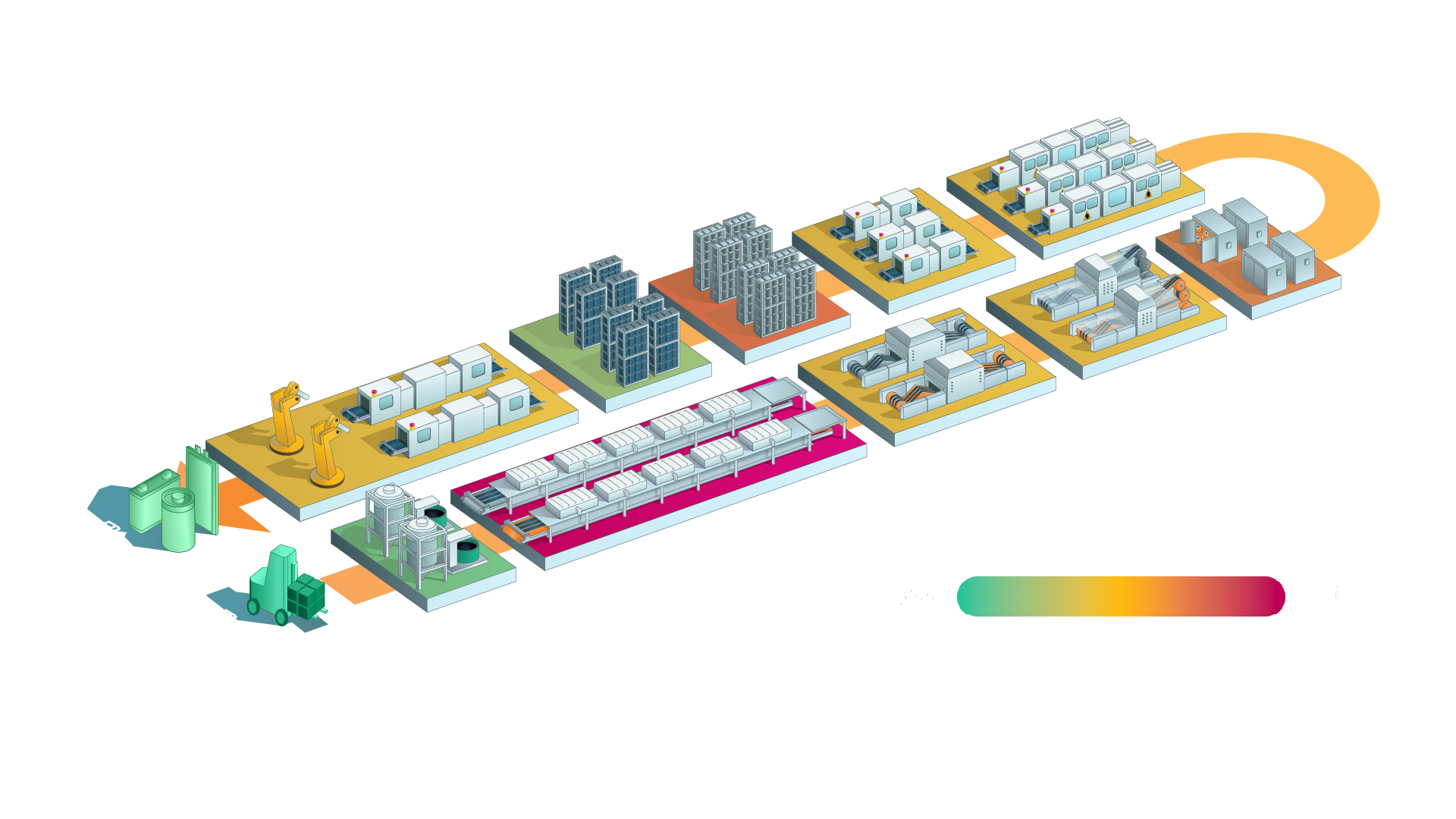
The production of battery cells requires a significant amount of energy, including both electrical and thermal energy. Energy consumption in the production of battery cells can be divided into three phases:
- material extraction (mining and refining of raw materials)
- cell production (processing and transforming of the raw materials)
- cell assembly
These processes require a large amount of energy, particularly in the form of electricity and heat, to extract and refine the materials.
The main energy drivers for the red and orange/yellow-marked production steps are electricity for operating the systems and process control e.g. cooling systems or heating elements.
The energy cost of manufacturing battery cells, excluding the material mining and refining processes, ranges from 30 to 55 kWh of production energy per kWh of battery cell capacity.
Heatmap of Quality
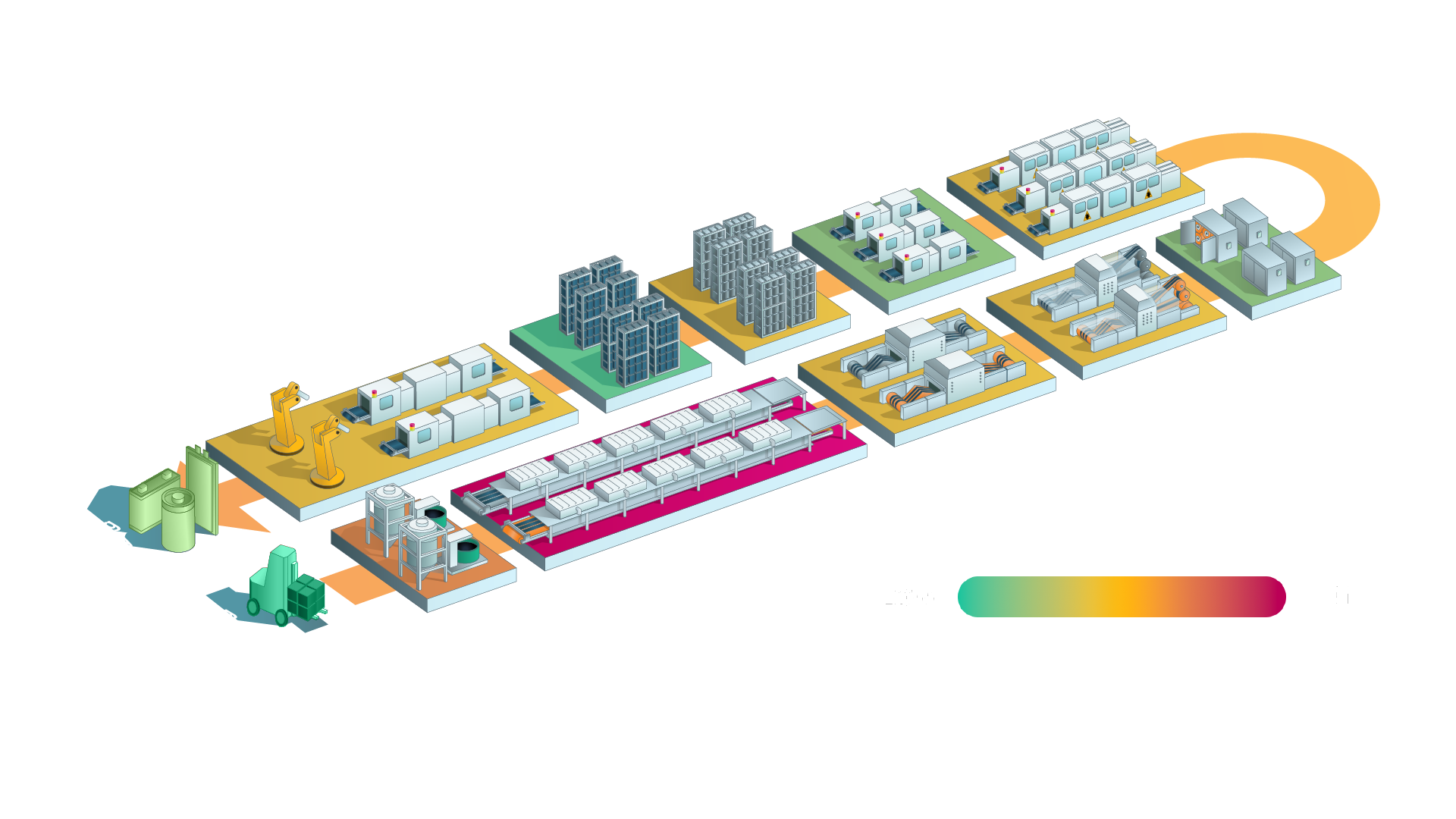
Reducing scrap plays an important role in the battery cell manufacturing. It not only has an impact on overall equipment effectiveness, but also on sustainability and competitive position in the market. Through targeted strategies such as process optimization, material recycling, and strict quality control, manufacturers can effectively reduce the amount of waste while improving the use of resources.
The scrap rate percentage for the battery cell production process ranges from 3% to 32%.
Material waste (e.g. due to material defects or trimming) and equipment malfunctions are the main causes of the scrap rates in the production steps.
Heatmap of Clean and Dry Rooms
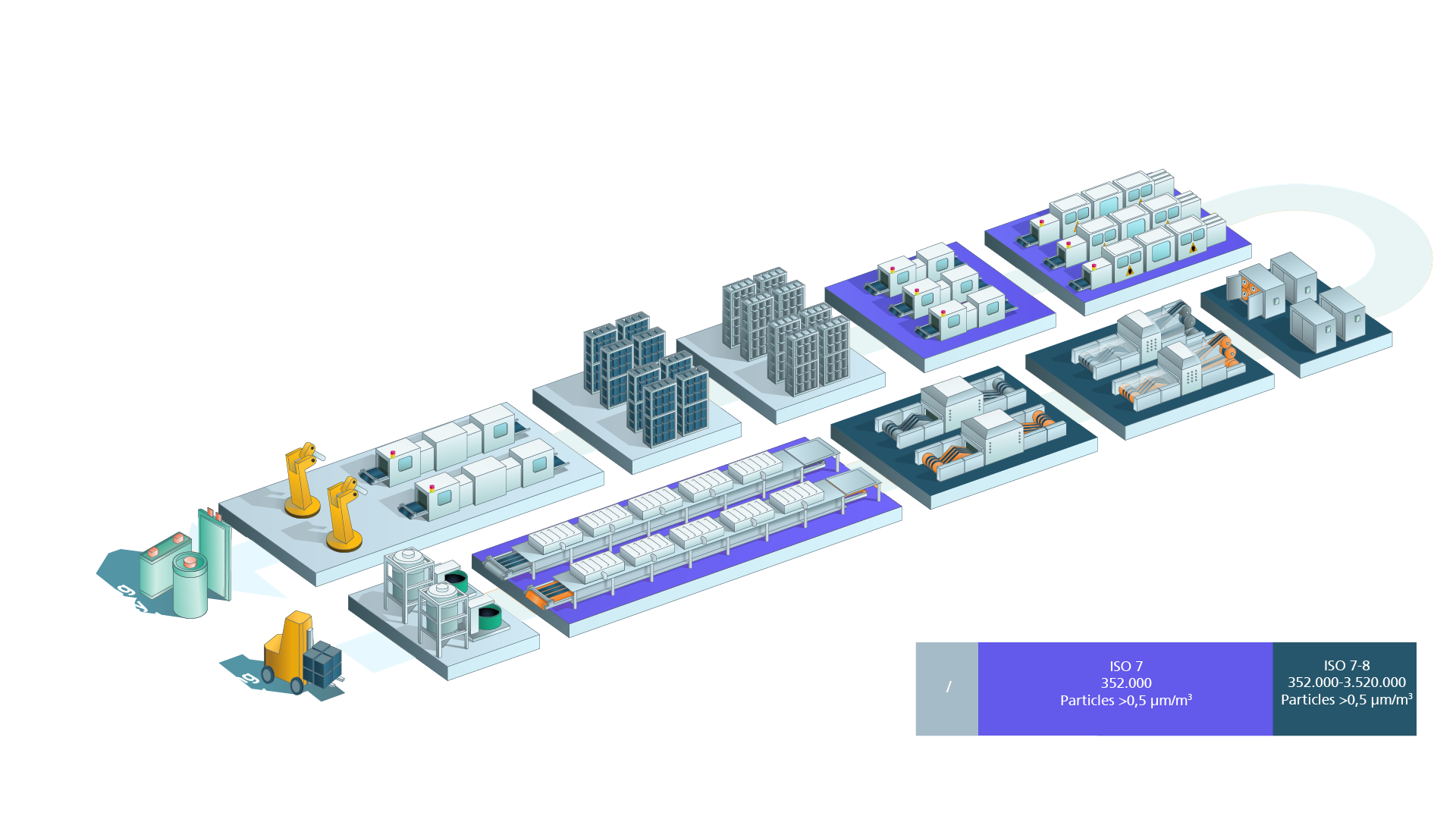
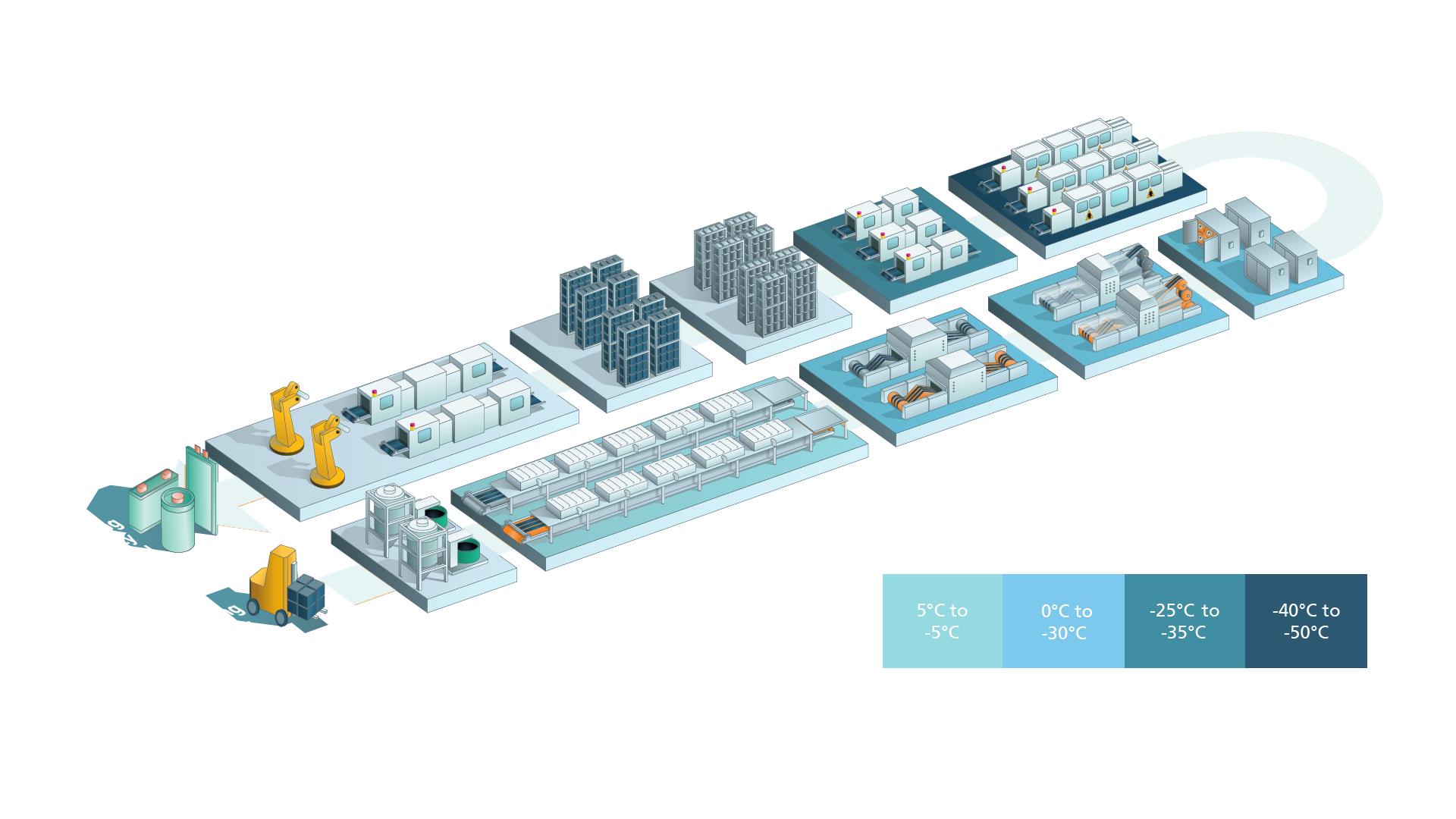
Clean and dry rooms ensure the quality and performance of the manufactured battery cells in several production steps. A dry room is a controlled environment with extremely low humidity, which is necessary to protect sensitive materials from moisture. These materials can react upon contact with water, which can affect the performance of the battery cells or even render them unusable.
Clean rooms, on the other hand, provide an environment with minimal contamination from dust, particles, and microorganisms. In battery cell production, it is important that the production areas are free of such contaminants to avoid short circuits, chemical reactions, and other defects that could affect the safety and efficiency of the battery cells.
The use of clean and dry rooms ensures high product quality, which is crucial for the performance and longevity of modern batteries, especially in electromobility and other high-tech applications.